Methoden der Risikobeurteilung im Maschinenbau
Es gibt nicht diese eine und einzige perfekte Methode zur Risikobeurteilung. Vielmehr haben sich trotz aller Normen und Richtlinien viele verschiedene Methoden entwickelt, die mit unterschiedlichen Stärken und Schwächen glänzen können. Bei der Risikobeurteilung der verschiedensten Produkte und Maschinen ist nicht vorgeschrieben, wann welche Methode verwendet werden soll. Der Hersteller und dessen Konstrukteure haben die freie Wahl.
Weiteres zur Risikobeurteilung:
Ansonsten helfen wir Ihnen auch gerne persönlich weiter:
Es gibt eine lange Liste an Methoden und Verfahren, die gegenüber anderen als zweckmäßiger gelten. Fünf Beispiele zweckmäßiger Methoden sind:
- WHAT-IF Methode – WAS-WENN-Verfahren – Brainstorming
- FMEA-Methode – Fehlermöglichkeits- und Einfluss-Analyse
- FTA –Fehlerbaumanalyse
- HAZOP-Studie – PAAG-Verfahren
- Aufgabenbezogene Risikobeurteilung
WHAT-IF-Methode – WAS-WENN-Verfahren - Brainstorming
Die WHAT-IF-Methode – zu Deutsch WAS-WENN-Verfahren – gehört zu den Brainstorming-Methoden. Hier werden gezielt Fragen gestellt, beispielsweise zu den Auswirkungen des Ausfalls einer Maschinenkomponente.
Neben der Konstruktion und Steuerung der Maschine, ist auch die geplante Schutzeinrichtung Ziel der Fragen. Genauso werden Einflüsse der entweder verbauten oder von der Maschine zu verarbeitenden Werkstoffe und mögliche Fehler des Bedienpersonals berücksichtigt.
Brainstorming Methoden sind im Gegensatz zu anderen Methoden der Risikobeurteilung weniger strukturiert. Diese erste Risikoanalyse wird idealerweise von Fachleuten aus unterschiedlichsten Bereichen geführt und sollte ein Produkt von möglichst viele Seiten betrachten. Ein WAS-WENN-Brainstorming sollte vor allem als Vorbereitung für eine formelle Risikobeurteilung gesehen werden.
Vorteil: Mit Hilfe von Brainstorming werden bei neuen Produkten schnelle Ergebnisse erzielt, die am Ende in der richtigen Risikobeurteilung miteinfließen können. Damit kann diese Methode schon im Vorfeld wichtige Ergebnisse liefern und für kommende Probleme sensibilisieren.
Nachteil: Diese Methode der Risikobeurteilung beansprucht recht viel Zeit, gemessen am ergebnis. Brainstorming alleine reicht jedenfalls nicht aus: Diese Methode sollte stets mit anderen Risikobeurteilungs-Methoden kombiniert werden, damit in der Risikoanalyse keine Gefährdungen übersehen werden.
FMEA-Methode – Fehlermöglichkeits- und Einflussanalyse
Mit der FMEA-Methode – Kurzform für „Failure Mode and Effects Analysis“ oder zu Deutsch Fehlermöglichkeits- und Einfluss-Analyse – werden Lebensphasen und Arbeitsschritte auf Fehler überprüft und die Ursachen und daraus resultierenden Folgen festgehalten.
In der Risikoanalyse dieser Methode werden die Fehler nach ihrer Bedeutung, der Wahrscheinlichkeit ihres Auftretens und der Entdeckungswahrscheinlichkeit sortiert. Im Anschluss daran können Maßnahmen unternommen werden, die zur Risikominderung beitragen und die Auswirkungen der ermittelten Fehler eindämmen.
Bei der FMEA Methode haben Konstrukteure eine nahezu freie Wahl beim Detailierungsgrad. Analyseergebnisse können in weiteren Untersuchungen zum selben Thema als Ausgangsinformationen dienen.
Vorteil: Mit FMEA können Risikoanalysen bei Bedarf sehr weit ins Detail gehen und das Produkt von allen denkbaren Seiten beleuchten. Diese Methode zur Risikobeurteilung eignet sich also besonders bei der Untersuchung von Baugruppen, Bauteilen, Funktionen und Prozessen.
Nachteil: Dieser Methode sind vor allem dann Grenzen gesetzt, wenn das Budget begrenzt ist. Je detaillierter die Untersuchung des Produkts sein soll, desto höher sind Zeit- und Personalaufwand. Dennoch hat sich die FMEA-Methode bewährt und ist in der Risikobeurteilung zu einem Standard geworden.
FTA – Fehlerbaumanalyse
Bei der „Fault Tree Analysis“ – kurz FTA oder auf Deutsch „Fehlerbaumanalyse“ – werden mögliche Risiken in einer Baumstruktur dokumentiert. Bei dieser Methode der Risikobeurteilung bekommt jedes Hauptereignis einen eigenen Baum. Dieses Hauptereignis bildet die Spitze des Fehlerbaums ab und kann einen Funktionsausfall darstellen oder die Auswirkung davon. Eine Auswirkung kann ein Unfall an der Maschine darstellen, welcher zu einer Verletzung des Maschinenbedieners führt. Die ermittelten Ursachen und Unfallarten werden darunter angeordnet.
Um der Ursache des Hauptereignisses weiter auf den Grund zu gehen, kann jede dieser Ursachen und Ausfallarten weiter verfolgt werden.
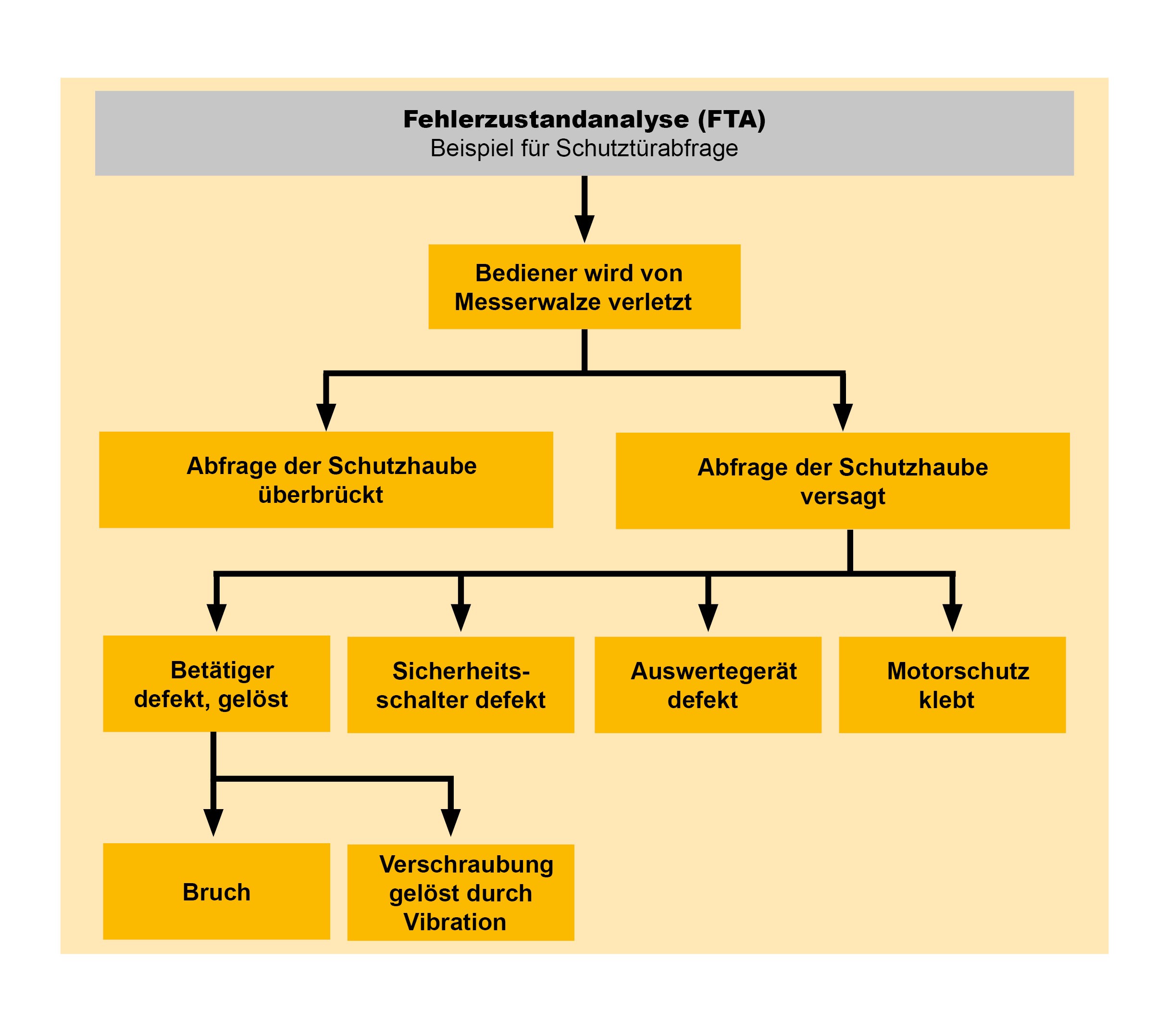
Vorteil: Durch die Darstellung als Baum werden Wirkungszusammenhänge verständlich dargestellt. Die Fehlerbaumanalyse ermöglicht außerdem eine tiefergehende Betrachtung eines Ereignisses und eine genaue Nachprüfung der Komponente, die das Ereignis verursacht hat.
Nachteil: In dieser Risikobeurteilung hat jedes Hauptereignis seinen eigenen Fehlerbaum. Ähnlich wie bei der FMEA-Methode werden also große Mengen an Zeit und Ressourcen in Anspruch genommen, um alle Ereignisse abzubilden. Zusätzlich hierzu können nur alle bekannten, dafür jedoch keine unbekannten Fehler und Ereignisse untersucht werden.
HAZOP-Studie – PAAG-Verfahren
Die HAZOP-Analyse – vom Englischen „Hazard and Operabilitiy“ – ist eine weitere Methode zur Risikobeurteilung. Das PAAG-Verfahren ist das deutschsprachige Pendant hierzu und ist Abkürzung für Prognose, Auffinden der Ursachen, Abschätzen der Auswirkungen und Gegenmaßnahmen.
Die zu untersuchende Maschine wird zunächst anhand der Abläufe und Funktionen definiert. Im Anschluss werden Ziele festgelegt, die mit der HAZOP Studie erreicht werden sollen: Zum Beispiel eine höhere Bedienersicherheit oder Zuverlässigkeit der Maschine im Produkt-Betrieb oder um Fragen zu den Umweltauswirkungen zu klären.
Um die Leitworte letztendlich passend einsetzen zu können, braucht es eine sinnvolle Unterteilung der Maschine in Einzelfunktionen, Prozessschritte oder den Tätigkeiten in verschiedenen Lebensphasen. Abweichungen werden im Anschluss untersucht und deren Ursachen und Auswirkungen bestimmt. Maßnahmen zur Verringerung von Abweichungen werden in der Untersuchung ebenfalls festgehalten.
Vorteil: Abweichungen des Produkts lassen sich mit Hilfe der Leitworte („zu gering“, „zu hoch“, usw.) einfacher feststellen. Die Gefahr bei der HAZOP-Methode, Abweichungen in der Risikobeurteilung zu übersehen, ist sehr gering.
Nachteil: HAZOP ist denkbar ungeeignet für Maschinen, die sich in der frühen Phase der Entwicklung und Konstruktion befinden und Funktionen und Bestandteile noch nicht eindeutig definiert sind. Der sinnvolle Einsatz dieser Methode zur Risikobeurteilung ist also stark eingeschränkt.
Aufgabenbezogene Risikobeurteilung
Die Aufgabenbezogene Risikobeurteilung wird von der Norm DIN EN ISO 12100 – Sicherheit von Maschinen empfohlen und ist damit ein Standard im Maschinenbau. Hierbei wird das Produktleben in verschiedene Lebensphasen aufgeteilt. Diese Lebensphasen, die in Transport, Lagerung, Inbetriebnahme, Betrieb, Wartung und Entsorgung aufgeteilt werden, werden nochmals in Aufgaben aufgeteilt. Diese enthalten Tätigkeiten von Personen sowie automatische Abläufe und Situationen.
Nach dieser Aufteilung werden Aufgaben untersucht und mögliche Risiken und Folgen der Gefährdungen definiert. Auf Grundlage dieser Gefährdungen werden schließlich Lösungsansätze und potentielle Maßnahmen zur Risikominderung entwickelt und dokumentiert.
Vorteile: Da bei der aufgabenbezogenen Risikobeurteilung alle Lebensphasen und mögliche involvierte Tätigkeiten von Personen berücksichtigt werden, ist diese Risikobeurteilungsmethode vielseitig einsetzbar und besonders im Maschinenbau, bei elektrischen Apparaten oder Medizingeräten geeignet.
Nachteile: Weniger geeignet ist diese Methode bei verfahrenstechnischen Anlagen oder solchen, die überwiegend automatisch arbeiten.
Neben den hier genannten gibt es noch etliche weitere Methoden zur Risikobeurteilung. Die eine perfekte gibt es jedenfalls nicht: In manchen Fällen lohnt es sich also, mehrere Methoden zu verbinden, um deren Schwäche auszugleichen.
Sie haben noch Fragen? Dann nehmen Sie mit uns Kontakt auf: